NO. |
photo |
report |
1 |
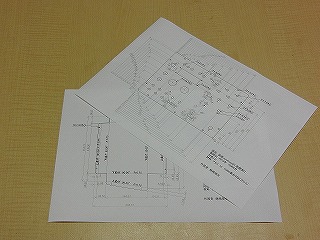 |
受信機外装の部品図です。
これをもとに加工機の特性等を教えていただき、さらなる改良をすることになりました。
|
2 |
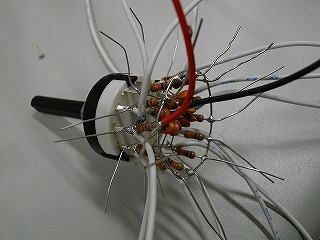 |
12接点スイッチ。なぜ買ったのだろうか。
チャタリング防止等の機能を付けるために、必要以上に配線に苦労したのだ。主に星野が。
しかも、実際はこんなに抵抗はいらなかったとかなんとか。
お疲れ様です。
|
3 |
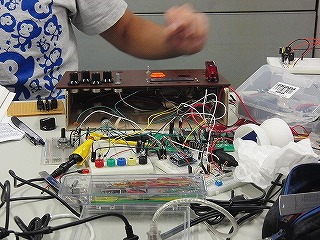 |
受信機の箱部分を段ボールで作り、配線を行った。
|
4 |
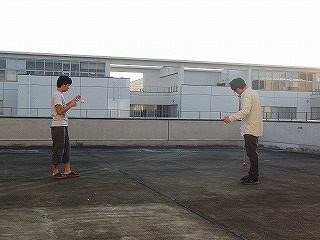 |
時々こうやってヨーヨーの練習をしています。
どうも、大学の1年生が、ヨーヨー部をつくろう等と動いているようです。
プレイヤーが増えることはいいことですね。
|
5 |
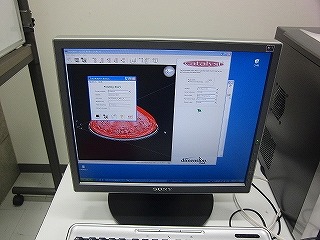 |
基板搭載用の専用ヨーヨーを、とりあえず3Dプリンタで作ろうと思いました。
この時3Dプリンタが予想外の機能停止に陥り、途方に暮れることになりました。
仕方ないのでその他の手段を用いることにしました。
様々な加工機、加工法が試せるのがものつくり大学のいいところです。このピンチは何とか切り抜けられました。
|
6 |
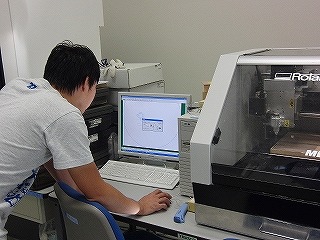 |
基板を切削で作ります。
デザインスパークで設計した図面を、どの様にMDX40に受け渡すか、そこの調整に非常に苦労しています。
|
7 |
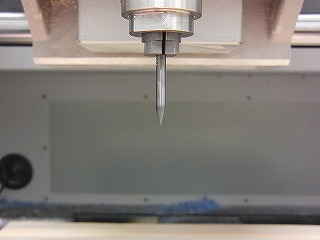 |
切削に使用するのは直径0.1mmや0.2mm等の極小径のエンドミルです。
思いのほか安く買えるんですね、エンドミル。例えば0.1mm径でも1000円から2000円で買えます。
10000円以上するものだと思い込んでいました。
|
8 |
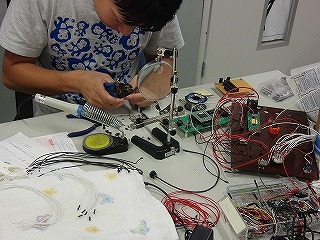 |
SHマイコンとスイッチ類を接続するために、配線をします。
|
9 |
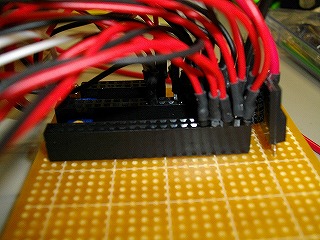 |
3端子レギュレータとACアダプタで、5Vと3Vの電源を取れるようにする装置です。
スイッチ類はここを経由してマイコンと連携を取ります。
|
10 |
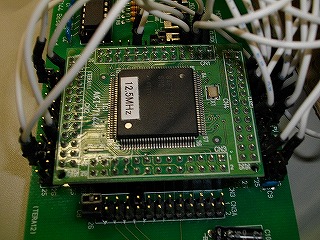 |
SHマイコンに配線している様子です。
|
11 |
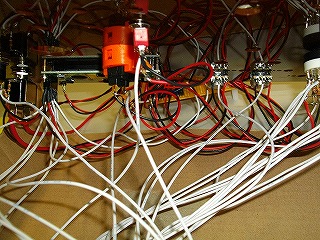 |
受信機内部です。
配線だけでおなかいっぱい。
マイコンもXBeeも電源も箱の中に入りませんでした。
|
12 |
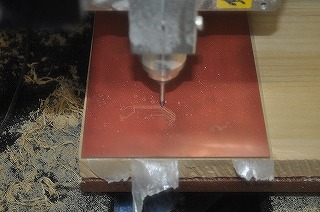 |
基板の切削を始めました。
数々の切削テストを行い、デザインスパークで作った回路図から切削用パスを作ることに成功しました。
|
13 |
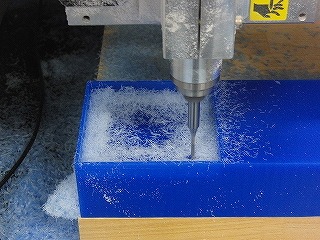 |
3Dプリンタが故障中の今、簡単にヨーヨーの外形を作れるのは、サンモジュールSSの切削しかない!
しかし、サンモジュールSSは密度が非常に小さいので、外周に重りを付ける必要がありそうだ。
これは、そんな重りを作るためのゴム型を作るための型をワックスの削り出しで作っているところ。
|
14 |
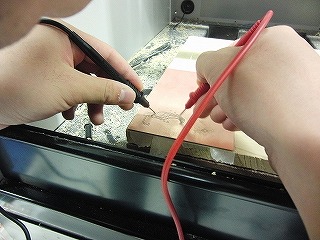 |
切削した基板にエラーが無いかチェックします。
エラーがあったらそこだけ削り直しです。
|
15 |
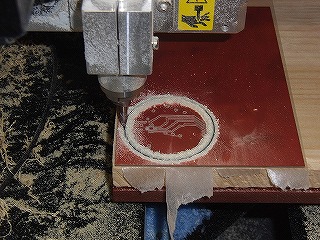 |
導通チェックがOKだったので、基板の抜き出しを行います。
直径0.5mmのエンドミルでいっきに削りぬいてしまいます。
|
16 |
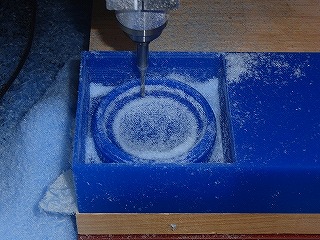 |
型切削も終盤。
この枠の中に耐熱シリコンを流し込んで型を作ります。
|
17 |
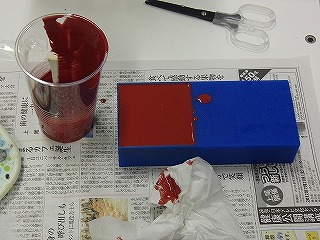 |
約300度まで耐えられる耐熱シリコン。
これでウェイトリングを複数作ることが出来ます。
ちなみに、使用する合金はPb-Sn合金です。
いわゆる活字合金と呼ばれるもので、低融点で収縮が少なく、密度が高いのが特徴です。
|
NO. |
photo |
report |
1 |
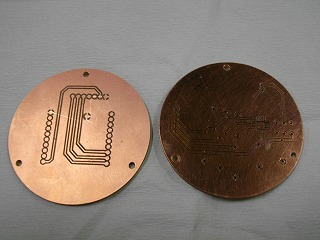 |
基板が出来上がりました!画像は左が、出来上がった状態、右が穴開けして、コンパウンドで磨いた状態です(なんとなく鏡面にしてみました)。
何度かのテストでなんとなく加工条件等が定まってきたので、これからは安定して作れそうな感じはあります。
ただ一枚に24時間以上(30時間くらい)かかってしまうので計画性を持って作っていきたいところです。 |
2 |
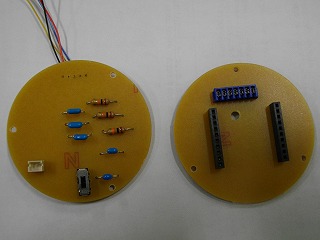 |
部品付けをします。とてもシンプル。最低限の動作だけの回路なので、まだ部品点数は少ないです。
|
3 |
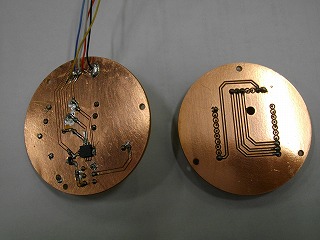 |
裏面です。とても汚いです。パターンの溝が極細なので、はんだがブリッチしないよう注意を払います。
特に加速度センサのピンがLFCSPタイプなためがんばってはんだ付けします。
電源を入れる前にショートしてる所がないかチェックして完成です!
|
4 |
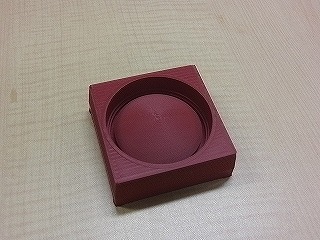 |
耐熱シリコンによるゴム型。
底の方の深さ3mm程度を利用する。
ちょっと無駄に使いすぎた。
|
5 |
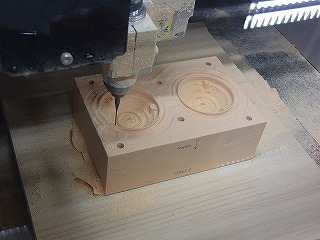 |
サンモジュールを削り出してヨーヨーを作っているところ。
何かと大活躍なMDX40。
|
6 |
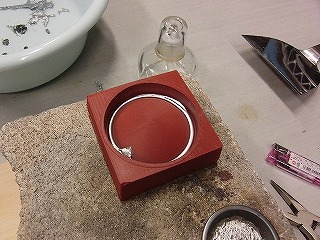 |
低融点合金(以下活字合金)を流し込んでみました。
表面張力で表面が膨らんでしまい、失敗。
|
7 |
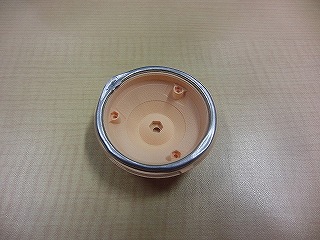 |
ウェイトリングをサンモジュールヨーヨーに装着してみました。
やはり表面張力で表面が膨らみすぎてます。
|
8 |
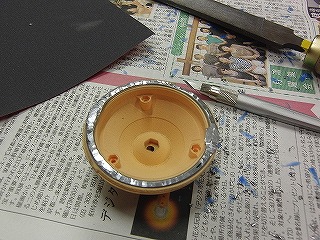 |
活字合金をカッターややすりで削って小さくしています。
諦めました。
|
9 |
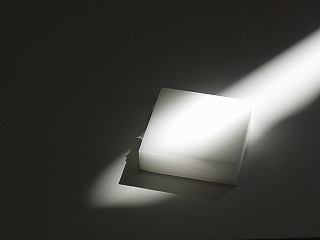 |
厚み8mmのポリアセタール片。
もともとは1辺が300mmの長方形の板材でした。
レーザー彫刻機で両面からカットして無理やり小片にしました。
これをベースに軸周りの部品を作ります。サンモジュールじゃ心もとないのです。
|
10 |
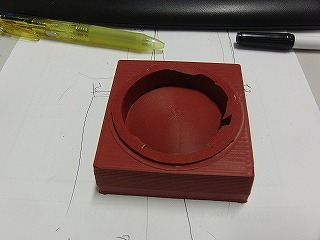 |
ゴム型にふたを作りました。
これで表面が平らになるはず。
|
11 |
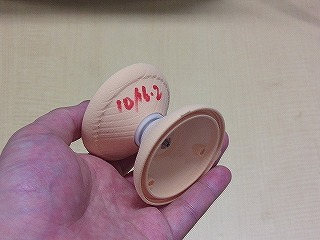 |
あり物でサンモジュールヨーヨーを仮組しました。
サンモジュールはケミカルウッドと呼ばれる木材で、今回使用した物はサンモジュールSSという、非常に密度の軽いものです。
切削性はいいのですが、その分強度もなく、今回の場合、6角穴(アクセル固定用)がなめてしまって大変でした。
|
12 |
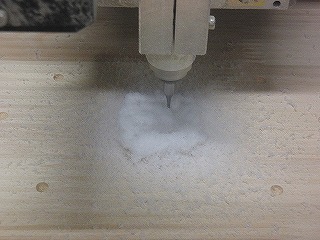 |
ポリアセタール製フランジの加工を行っています。
|
13 |
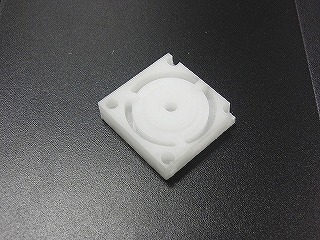 |
ポリアセタール製フランジの片面です。
反対面を削って完成!
|
14 |
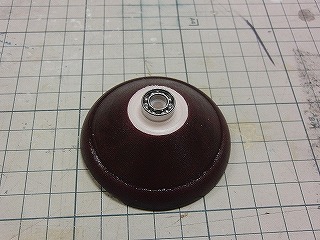 |
ポリアセタール製フランジを装着しました。
色も、ニスを塗って付けました。
|
15 |
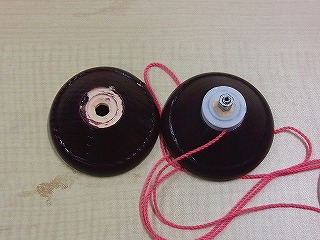 |
スローした瞬間割れました。
サンモジュールSSは、一筋縄ではいかなさそうです。
|
16 |
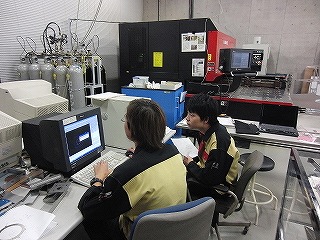 |
話は変わって、受信機盤面製作の図。
t2アルミ板をレーザー加工機で切り出します。
とりあえず、各種部品が設計した穴で切り出せるか確認します。
|
17 |
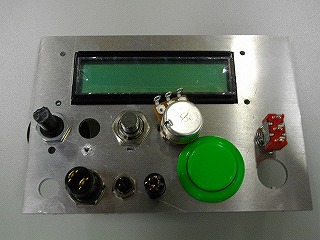 |
切り抜いたアルミ板に各種スイッチ類を装着。
入っていないところは穴のサイズが合わなかったものです。
後日再調整して穴を確認します。
|
18 |
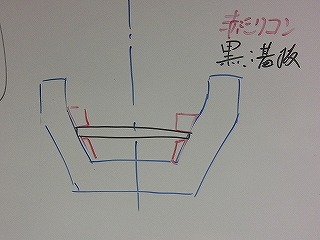 |
自作ヨーヨーじゃ精度が出なくて、トリックしにくい。
ということでアタッチメントタイプも視野に入れ始めました。
|
19 |
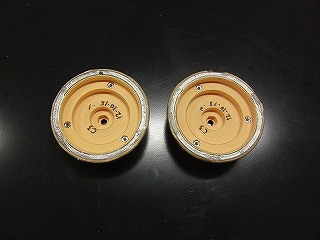 |
サンモジュールボディに、表面張力の問題を克服したウェイトリングを載せました。
|
20 |
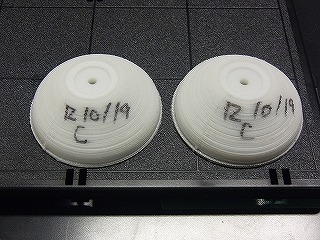 |
サンモジュールじゃぶれがひどいということで、困った末に、故障中の3Dプリンタを試したところ、特定条件下で動くことが分かりました。
しかし、仕上がりがひどいです。
|
21 |
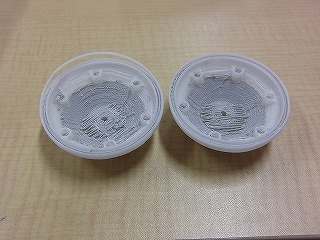 |
サポート材をかみこんでしまい、また薄肉部がバラけてしまい、使い物になりませんでした。
|
22 |
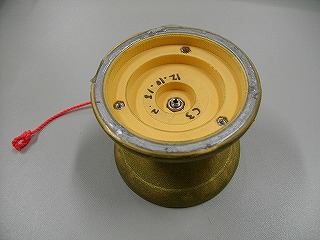 |
適当にそこら辺にあったゴールドスプレーで色を付けたら、乗りが悪くて汚くなった。
|
23 |
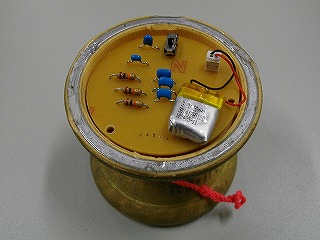 |
サンモジュール製ボディに基板を装着。
重心が極めて偏っており、まわしにくいコトこのうえなし…
産業廃棄物の出来上がりです。
|
24 |
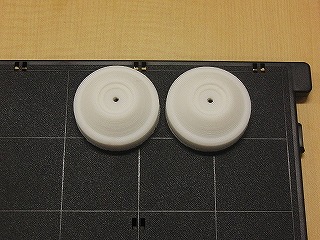 |
薄肉部を減らし、不調の3Dプリンタでも大丈夫な形状を設計したよーよー。
なんとか出力出来て良かった。
|
25 |
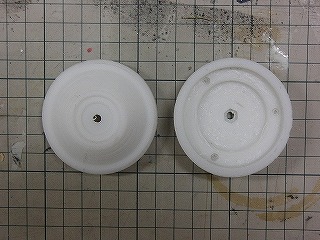 |
基板を載せるために段差がある。
|
26 |
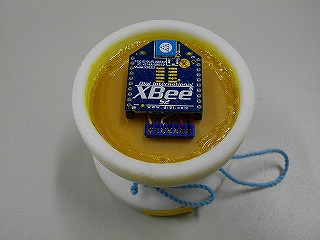 |
ナットが接着出来なかったので、基板を直接接着してしまった。
|
27 |
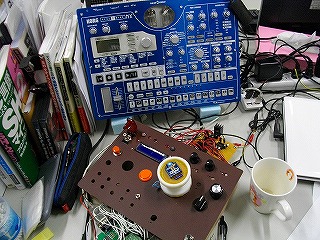 |
演奏するもの一式。
|
NO. |
photo |
report |
1 |
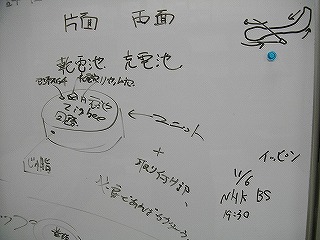 |
自作ヨーヨーのボディでは、精度がでねーぞXXX!!
ってことでアタッチメントの開発も同時進行で作っていきます。
市販ヨーヨーにくっつけて使用出来るものを目指します。
|
2 |
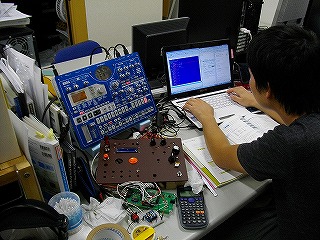 |
最終的に楽器として利用するためには、プログラミングが肝になってきます。
星野も飯嶋も、プログラミングはあまり得意ではないのでかなり苦戦しています。
|
3 |
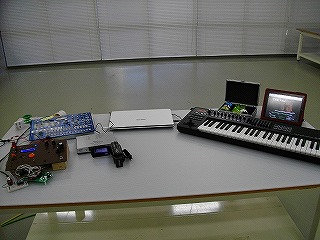 |
第8回全国手づくり楽器アイデアコンテストに応募すべく、ビデオ審査用の映像を撮影します。
かっこつけたつもり。
ちなみにこの段階で、プログラミングされた音がヨーヨーの動きに合わせて順番になるようになっています。
|
4 |
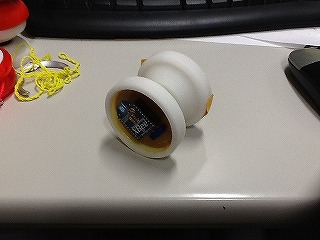 |
故障中の3Dプリンタを無理やり使って作りました。
手づくり楽器アイデアコンテストのビデオ審査はこの状態で応募しました。
これ以降3Dプリンタが動いたところを見た者はだれもいない・・・
|
5 |
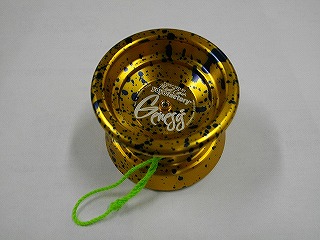 |
この「ジェネシス リランチ」に基板をアタッチできるようにします。
研究費でヨーヨーを買うのは、これで5個目かな?
しかしこれは高い買い物であった。
改造します。
|
6 |
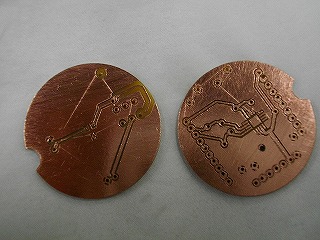 |
POMを切削して作る予定の新型ヨーヨーに搭載する小型基板です。
以前のものは直径50mmでしたが、今回は34mmにまで縮小。
結局これをジェネシスに乗せることになりました。
|
7 |
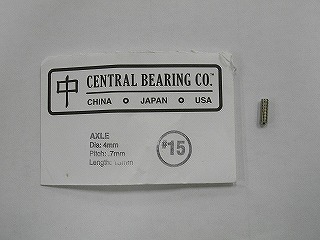 |
ジェネシスのアクセルに対応した物を購入。
ジェネシスに乗せる基板の両側が連携しなくてはならないので、穴をあけます。
|
8 |
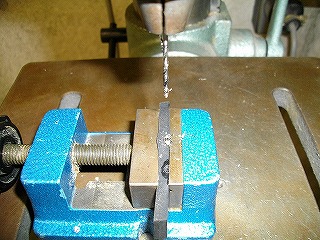 |
治具を作って旋盤でやろうと、飯嶋は渋りましたが、星野がボール盤で強行。
案外あっさり穴があきました。
穴径は直径1.8mm
|
9 |
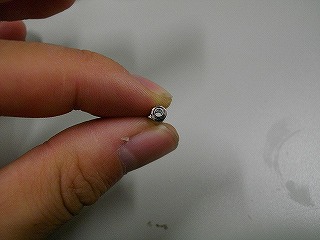 |
穴空きアクセル
|
10 |
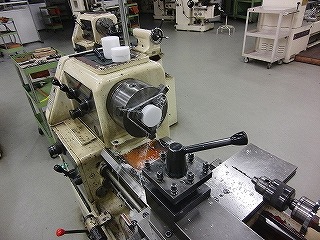 |
POMの切削はMDX40で行いますが、その前に部材の切断や端面出しを行います。
これは端面出しの様子。
簡単に削れます。
|
11 |
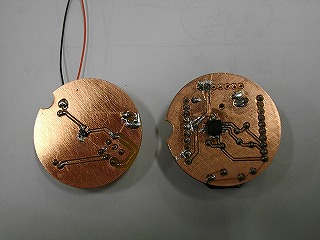 |
新型基板に実装できました。
|
12 |
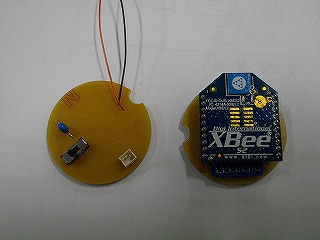 |
裏面です。
XBeeの裏側に加速度センサーが来ます。
図中左側にはバッテリーが載ります。
|
13 |
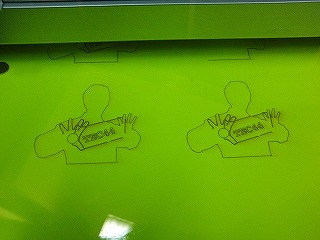 |
ステッカーをつくりました。
|
14 |
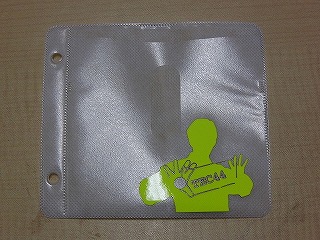 |
CDケースに貼り付けて、てづくり楽器アイデアコンテストに応募しました。
|